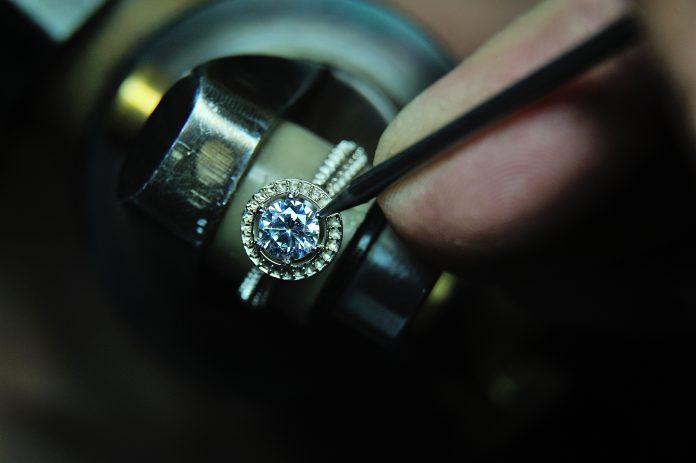
Stone-setting tools for lapidaries and a knowledge of the stone itself provide the right foundation for securing a gemstone in a metal fixture to best display the stone’s qualities, an essential jewelry-making skill.
Recently, I visited my cousin Doug Brandt’s jewelry studio, Collingwood Metalworks, to discuss what stone-setting tools should be included on a must-have list. A professional jeweler for over 40 years, Brandt offered ideas on tool essentials as well as building skills to the professional level.
Here are the seven tools that should be included in a stone setter’s workbox.
1. Ring Clamp
Brandt uses a GRS adjustable height bracket and ring clamp system that attaches to his workbench. A plate and cleat system allows the bracket to be adjusted to different heights depending on the individual project. The clamp itself can be swiveled, allowing the stone setter to keep the piece in the clamp and adjust it for ease of completing the setting. The piece of jewelry – usually a ring – can be tightened into the clamp between two heavy-duty pieces of plastic or leather so as not to scratch the item while working.
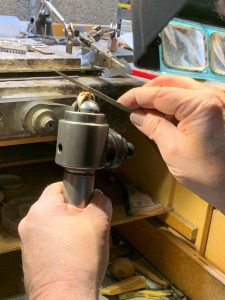
2. Burrs
Burrs give the stone setter many ways to prepare the seat for the stone. Heart-shaped burrs come in a variety of sizes for stones such as diamonds. The stone setter uses a heart-shaped burr to cut the seat or bearing – a notch between the prongs – where the stone snaps down. After cutting the seat, the stone snaps between the prongs. Brandt uses needle-nosed plyers to take the next step and begin forming the prongs around the seated stone.
Cup burrs also come in a variety of sizes and shapes. Inside the cup are tiny teeth. After the prongs have been brought down to a certain point over the stone, the cup burr fits the tops of the prongs rounding them over the stone and giving them a high polish. This is another step in dressing the prongs down over the stone.
3. Files
After a stone is seated in the prongs, a file will help sand the prongs down to meet the table or top of the stone. The stone setter needs to take great care to not scratch the stone with a handheld file or powered sanding disc. A barrette file only has teeth on one side and is designed to get very close to the stone without harming it. Brandt uses this file for dressing the prongs.
4. Mandril
Used primarily for determining the size of a ring, the mandril also comes in handy as a stone-setting tool. The mandril can be placed into a hole in the workbench and hold a ring while work is being done. Because the mandril is steel, it provides a steady place to maneuver a ring while adjusting prongs.
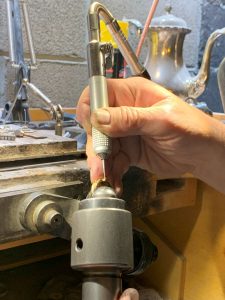
5. Flex Shaft Drill with Interchangeable Handpieces
Brandt appreciates the mobility of the flex shaft drill. Being able to move around a stationary piece using different drill heads allows him to use tools like the sanding disc to dress prongs. Operated with a foot pedal, the drill is efficient while requiring great care. The stone setter needs a good understanding of the stone and setting process so as not to scratch it with the sanding disc.
6. Channel Setting with Hammering Handpiece on the Flex Shaft
This tool allows the stone setter to use a drill-powered hammer to build or rebuild rails around a gemstone. The stone setter can get right on the edge with a hammer and pound the metal into place. While the stone setter can do this with the jewelry in the jaws of the GRP vice, another strategy is using the mandril. Metal on metal makes it easier to move the desired metal into position over a stone. For instance, a gold ring on the mandril will become more cooperative when hammered. The impact of metal on metal is greater if the stone setter understands the tolerances of the metal in which the stone is being set.
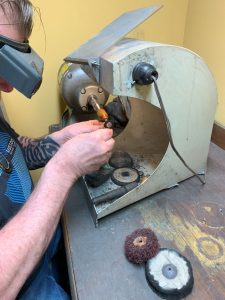
7. Polishing Machines
The polishing machine is an essential resource for taking a piece from tool marks to a high finish or high luster. Brandt uses soft bristle brushes or muslin buffs along with a cutting compound called Gray Star.
Through a process of different brushes and buffs, a jewelry maker can make scratches less visible, smooth out surfaces and increase shine. Brandt might move a piece from the soft bristle brushes to the muslin buffs as he works at smoothing and polishing to a high finish shine.
The types of metals being used also affect what brushes and buffs a jeweler might use. For example, different buffs and compounds are needed for platinum rather than gold. Platinum is more malleable than white gold, holds its shine longer and is naturally white. Made of mixed alloys, white gold needs to be replated over time and is more durable for everyday wear. All of these qualities and more impact the strategies for handling the two metals.
“At one time, platinum was highly sought after,” Brandt explained. “White gold was created to mimic platinum because it was more expensive. Today, gold is more expensive and more sought after.”
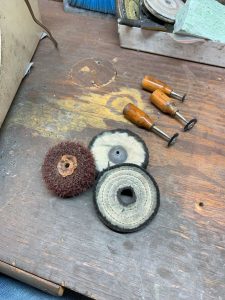
Designing Your Own Stone-Setting Tools
One of the tools Brandt uses while working on repairing a setting is a punch, he designed himself. He explained that in stone setting, sometimes you need specific stone-setting tools for your own practice. The punch he uses helps him adjust the prongs, tightening them down and over the stone.
Making his own stone-setting tools was part of Brandt’s early training. It was a good way to begin building the tools for his stone-setting practice. He also suggested finding used tools as a resource – he keeps an eye out for tools being sold from jewelers who are retiring or from estate sales. Not all stone-setting tools need to be brand new.
Margins of Error
To learn stone setting, Brandt suggests exploring an apprenticeship. It is hard to jump right into a professional stone setting, particularly faceted stones such as diamonds. While you may be able to use YouTube tutorials to learn some things, hands-on practice as an apprentice is invaluable to experience different types of stones and stone-setting projects plus gain a further understanding of the tools you need or prefer for projects. Experiencing diverse types of stones and different metals all while building skills with a wider array of tools under the supervision of a knowledgeable and skilled stone setter can be invaluable.
This story about stone-setting tools previously appeared in Rock & Gem magazine. Click here to subscribe. Story and pictures by Deb Brandt.