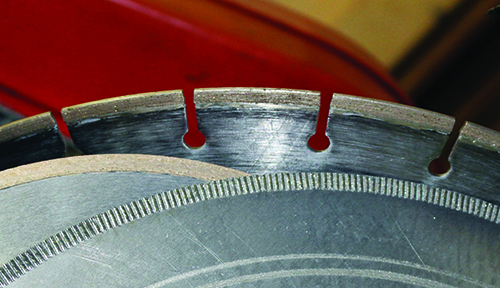
By Bob Rush
Frequently, on some social media sites as well as some forums, questions arise about the type of saw blades to buy for trimming or slabbing rock, and how to sharpen the blades.
There are three basic types of saw blades, notched rim, sintered rim, and segmented rim. In the past, the notched rim blades were the most common blades one would encounter. They are made by notching the rim of the blade blank and embedding the diamonds into the notches. These blades perform quite well.
Understanding Blade Performance
Advancements in blade manufacturing methods have resulted in a better performing blade. It is the continuous sintered rim blade. This type of blade is manufactured by mixing and bonding diamonds into a metal alloy and bonding that mixture together, under heat and pressure, to the outer rim of the blade core. This type of blade has superseded notched rim blades.
The final type of blade to consider is the segmented blade. These blades have notches manufactured into the rim. The notches consist of a slot into the rim with a round hole at the bottom of the slot. The slots provide a path for the coolant/lubricant to reach the rim more effectively and remove rock waste from the rim area. The blades are primarily utilized in larger sizes, beginning with 18 inches and larger.
Addressing Coolants
There also has been a lot of discussion about which coolants should be used on 10-inch trim saws. Many prefer to use water with additives because there is less mess during the cutting than when oil coolants are used. However, water isn’t a good coolant, because the flashpoint is quite low compared to the oils, which are commonly in use.
At the point of contact with the rock, the heat builds up, and for an instant, the water flashes to steam, which doesn’t carry the heat away. Most blade manufacturers do not recommend using water because it causes premature blade wear. However, many people prefer the easy cleanup of water, and with it, they endure the need for more frequent blade replacements.
Resharpening Techniques
When it comes time to resharpen a dull blade, there are numerous methods. As a blade is used, the diamonds in the rim abrade and break down, leaving small holes in the sintered areas of the cutting surface. The friction of the rock deforms this sintered alloy and moves the metal around, where it shields the existing diamonds, and the cutting action slows considerably.
Suggestions for handling this have included cutting through obsidian, which is ineffective and cutting through an old silicon carbide grinding wheel, which is a better approach.
John Rowland of Highland Park Lapidary, suggests turning a very coarse file sideways and strike the cutting edge of the blade vigorously around the diameter of the blade. This method is very effective in sharpening the blade.
However, the above-mentioned method doesn’t sharpen the sides of the cutting surface. By gripping the sides of the blade, you can feel the wider cutting portion on the sides of the blade.
If you can’t feel the wider area, the blade is worn out regardless of the remaining area of the diamonds around the rim. This step-up is required, so the blade cuts a slot, called the kerf, which is wider than the blade.
This must occur so the rock, which is the focus of the cut, doesn’t rub on the sides of the blade during the process. If the rock rubs the blade, the blade gets hot, the rock gets hot, and they both expand, binding the blade in the rock. These cutting surfaces do at least as much rock removal as the outer edge of the blade, thus they wear just like the outer rim.
My method to sharpen all the surfaces is to rub the outer rim vigorously sideways across the blade, with a piece of very coarse silicon carbide grinding wheel, followed by rubbing the sides of the blade vertically with the same grinding wheel piece.