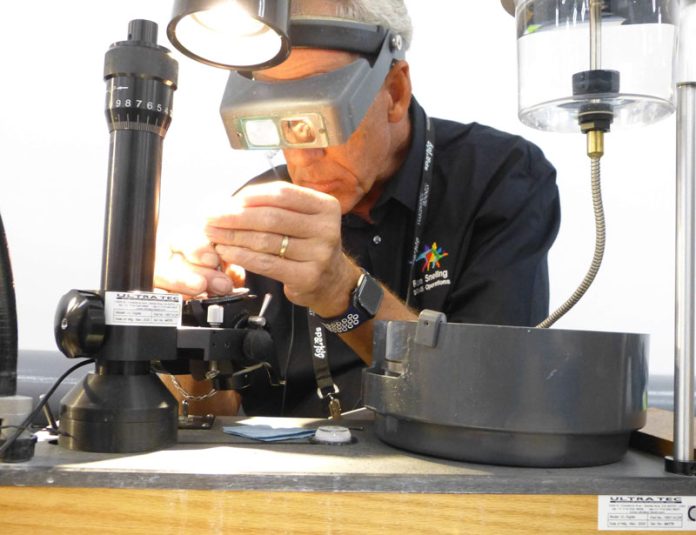
How to start gem cutting is something many ask. Luckily, lapidary artists have been around since humans walked the Earth and the field continues to grow. “This field is never going to go away. There’s always going to be an opportunity for someone to craft a jewel,” said Robert Mendoza, the production manager for ULTRA TEC. “I was in high school when Joe Rubin, ULTRA TEC’s president, and leader for over 50 years, allowed me to work side by side with him. He taught me so much.”
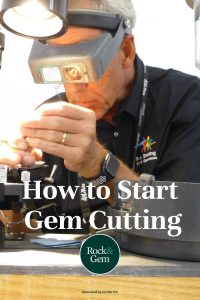
Robert said he can spot someone with what he calls the “gem-cutting gene” because of their questions and the way they examine a stone. These creative souls view the intrinsic worth of an object of beauty.
Reaching Younger Artists
Want to become a lapidarist? You’re in good company. Robert says they have noticed a younger demographic’s interest in cutting gemstones. Apprenticing for how to learn gem cutting is no longer a must. It’s now possible to learn from a myriad of sources granting more access to everyone.
Part of the reason so many gem cutters turn to ULTRA TEC is because of its solid foundation.
“We help them achieve the ideas they have in their mind. At the end of the day they have something tangible,” noted Mendoza. ”Joe Rubin started with a good design that we’ve been perfecting over the years. The ULTRA TEC V5 is the best machine to cut gemstones. It carries all the precision to cut gemstones.”
Continuing to Perfect
The ULTRA TEC team enjoys hearing from its customers and often innovates based on suggestions. An example is when they created a digital angle display (DAD) that reads to one-one hundredth of a degree.
“When you are gem cutting, you deal with a lot of angles. The key is to be able to repeat the angle every single time,” noted Robert. “No one else has one that dials down as precisely. We are very proud of this device.”
Quality & Versatility
Besides the quality and versatility of the design of the ULTRA TEC machines, people appreciate that while other faceting machine companies have come and gone, ULTRA TEC supports its people and products.
“ULTRA TEC is a traditional American company. Everything is done under one roof. This company is based on ethics, honesty, and integrity,” said Mendoza. “It makes people happy. We want them to enjoy the hobby.”
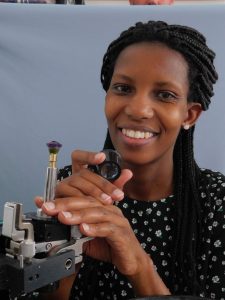
The Connection of Mine to Market – Noreen Masaki
Tanzania is known for gemstones, but if Noreen Masaki has her way, it will also be the hub of lapidaries.
“Tanzania is exceptionally rich in gemstone deposits of different varieties,” explained Noreen who has been teaching lapidary classes for over 20 years in Tanzania. Her goal, besides creating beautiful pieces, is to teach people to appreciate the relationship between the rough gem and the final product. This is relevant when it comes to encouraging artisans within her own country.
Her keen mind and excellent eye made her an exceptional student. “At that time learning about gems was a completely new thing to me,” she said. “At the end of the four weeks, I loved to work with gems.”
She said they used the ULTRA TEC V2 during her initial work. “What inspired me was the outcome of a faceted gem — the light reflection, colors, overall brilliance, and irresistible beauty. Over time I learned that not all gems which are cut show their beauty and brilliance and that it had something to do with optical laws and the type of machine used. I was lucky to learn precision faceting of gemstones with the best machine and from the best teacher who respected the optical laws and procedures.”
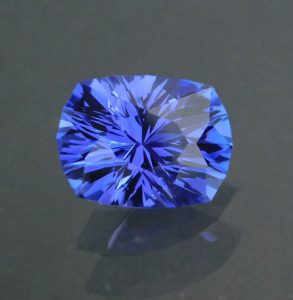
Current Work
Noreen now utilizes the ULTRA TEC V5 for her students and her own work.
Her students go home with a finished stone on their first day and much of this is because of the quality of the machine.
“I’ve tried so many (different machines),” she said. “The ULTRA TEC V5 is really precise. I do not need surprises when I cut my stones. I like the mast of the ULTRA TEC V5, especially the cheater that helps to find any facet if correction is needed.”
When Noreen works with a stone, she said, “I give priority of the pavilions first because they are responsible for the brilliance of the stone.” She said the drawback of cutting this way is to possibly cut more of the stone than she’d prefer if the angles aren’t spot on.
”We first cut it in our heads,” she said. ”I explain the laws of light reflection within the stone before you cut it. Each stone has its own properties. If the stone has a higher refraction index you cut it at lower angles.”
Noreen sees the beauty in her stones, as well as her students, and through her exceptional talent and high-quality ULTRA TEC faceting machines, she’s creating a new generation of gemstone artists.
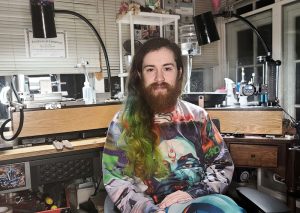
Answering the Call – Steven Tyler Manchini
Steven Tyler Manchini, also known as Steven Tyler the Designer, began making wire-wrapped jewelry in 2012 because “it allowed me to have a part-time job while I was in school.”
After obtaining his degree in biology, he continued making jewelry and exploring his creative side. A change in professions is not unusual for instance some go from tooth jewelry dentist to jeweler. “I love science, but every day I was there I was thinking about my bench,” Steven said.
Always Learning
Heeding his inner muse, Steven took classes and taught himself Gem Cad modeling to switch the direction of his vocation, including working with renowned designer Nolan Sponsler who taught him the art of faceting. “I’m learning as much as I can. We all share the knowledge,” he said.
The desire to learn pays off for everyone who marvels at Steven’s unique vision when gem cutting and creating jewelry. A combination of talent and dedication is the perfect recipe for one-of-a-kind pieces.
“I sit at my bench eight to 14 hours a day. I work seven days a week,” he said. ”I just sit at my bench and start the process. It’s the passion for the work that’s driving it.” He believes it’s a matter of being present and finding inspiration in the basic steps as much as anything.
“All the geometry and geometric stuff are what inspired me,” he said. “I love the Fantasy machine from ULTRA TEC. As much as I love flat faceting, the Fantasy machine inspires me.”
The Fantasy machine gives him the latitude needed to explore the geometric patterns that catch his eye. “I like the build of the machine,” Steven commented. “It has an infinite amount of styles that you can do. I had to splurge.”
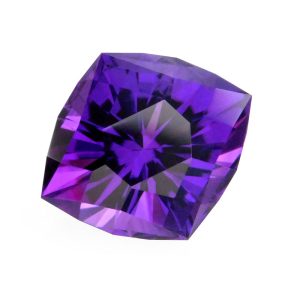
Professional Goals & Favorite Gems
Steven’s goal of having a piece in a museum was realized as his piece “Alsace Aurea” (the Golden Moose) was accepted in the Maine Mineral and Gem Museum’s “Big Find” event.
Steven cut a rare 25-carat, bi-color Maine tourmaline from the Dunton Gem Quarry and off-set it with two, locally sourced, tourmalines cut with the ULTRA TEC Fantasy machine. They are all set in golden moose antlers creating the ultimate celebration of New England jewelry.
Although it’s like choosing a favorite child to pick preferred gemstones, as a true New Englander, Steven appreciates working with regional specimens. “I really like tourmaline. You can do a lot with it.”
Every generation brings something new to the cutting bench, and Steven offers an artist’s eye with a scientist’s attention to detail that breathes life into his one-of-a-kind gemstone designs.
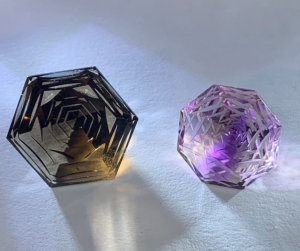
Representing Quality – Ron Snelling
Ron Snelling’s interest in gem cutting began in the mid-1960s when the parents of his future wife started a local rock club. He is now the Colorado representative for ULTRA TEC and still belongs to a rock club. “I am one of the cutters in the group. I do not dig in the dirt,” he laughed.
Ron purchased his first ULTRA TEC in 1990 and is an admirer of the company and its products. “They keep upgrading and offering parts,” he said, including supporting the longtime workhorse, the V2, which emerged on the market nearly 50 years ago. The reality is that ULTRA TEC machines don’t become obsolete, the company simply continues to improve designs to meet the customers’ needs.
“My favorite is the VL (Classic),” Ron noted. “I got to be part of the research and development and put in a little information, among other experts, to build it.” He also owns an ULTRA TEC V5 and a Fantasy machine making him the ideal person to talk to lapidaries about what they want to do with their designs.
Ron is happy to share his knowledge about how to best adjust the machines for a given task. Whenever someone has a question in his region, he is the expert with the answers. “I do enjoy sharing this,” he commented.
The Hook & Acalling
Ron said one of the most amazing steps in cutting a gem is when the stone is finished and the cutter removes the wax, allowing the gemstone to come to life. “That’s probably the hook (for this hobby),” he mused.
Over the years Ron found his calling in bringing already-cut gems back to life. “A friend has a jewelry store and asked me if I could do repairs,” he said. “Sometimes there are stones, like tanzanite, that are pretty beat up. When you resurface it, the color comes back into it. The best part of all of this is repairs have paid for my hobby and my equipment.”
Hobby Trends
Ron has noticed a trend in the hobby. “It’s interesting how the popularity has gone up. What we’re seeing is a resurgence of 20-somethings.” He noted some amazingly talented younger artists are entering top-notch competitions and winning.
At one point there was more of a feeling of competition and some degree of secrecy in techniques in the gem-cutting community. But Ron said he views gem cutting like music. “There are only so many chords to play, but there are different ways to play them. You need to play it your own way.”
While Ron often works with whatever gemstones need his attention the most, he said given the chance to work with a certain variety, “I probably enjoy quartz the most because they’re large, they’re plentiful and you can do so much with them.”
This story about how to start gem cutting previously appeared in Rock & Gem magazine. Click here to subscribe. Story by Amy Grisak. Sponsored by ULTRA TEC.