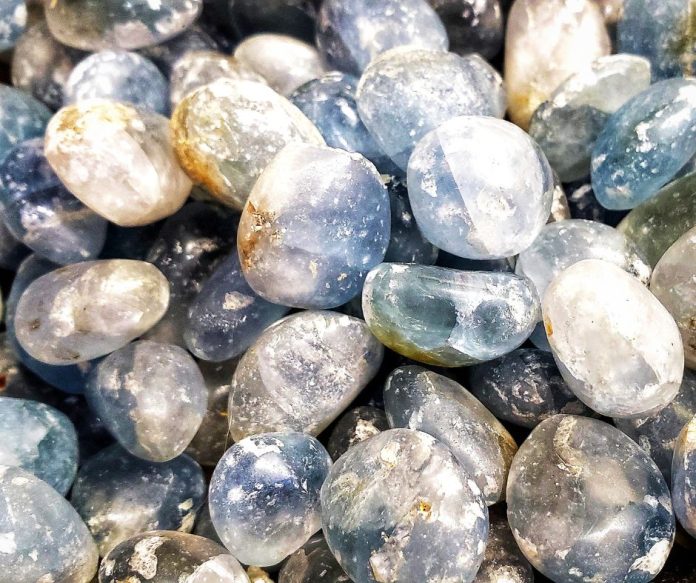
Polished rocks are gems that many love to create, sell or collect. Tumblers have the experience to make their gems shine. Here’s their advice to make the most of your rocks.
Kagayaku is Japanese for “shine” and in the history of lapidary, few cultures have been more intimately acquainted with polishing rocks and stones than Japan, where early examples, honed primarily into tools like axes, date back 30,000 years.
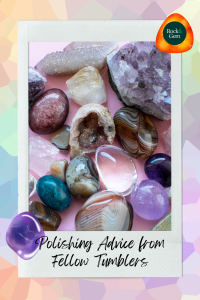
Shining History
Polishing rough-cut stone axes not only increased their intrinsic mechanical strength but created heads more readily capable of penetrating wood. Heritage Of Japan cites polished stone axes as intrinsic to clearing Neolithic forests for the introduction of large-scale crop and livestock farming.
We can also thank a region in Germany, Ider-Oberstein, for emerging in the 14th century as the “gem-cutting capital of the world.” Evolutions in the grinding wheel resulted in words like shinen, or schinen, entering the Old English lexicon and turning into what we use today: shine.
Agates, mined not far from these villages, were among the first raw stones cut into cabochons and carved gemstone sculptures, igniting greater demand for gem cutters and encouraging the migration of more stone carvers to Germany.
Polishing stones has helped hone human destiny so it’s little wonder that we “take a shine to” a gleaming finish.
From Raw to Polished Rocks
Some of the best beginner-friendly rocks for tumbling include agate, chalcedony, jasper, and quartz. All these (as well as petrified wood) are between five to seven, the ideal hardness on the Mohs scale of hardness, for rock tumbling success.
Before starting a polished rocks tumbling project though, it’s good to think of the end product and its shine. We’ve turned to experts in everything from tumbling supplies to jewelry crafting for suggestions on how to turn your raw stones into polished pieces ready to be worn, displayed, and appreciated for the roles they have played in history.
We’ve asked for the fastest, easiest, best, and most unusual ways to get a shine, plus what’s the most common question asked by beginners, and what’s the question they should be asking?
Fastest, Easiest, Best?
Two words, says John Leeds at J. Leeds Jewelry in Richmond, KY: Cerium (IV) Oxide. “It puts the ‘pop’ in,” he says about the professional lapidary polish. “Cerium oxide is good, super cerium oxide is best.”
Commonly used as a glass polisher, this oxide of rare earth metal, cerium, is excellent for polished rocks, including agate and quartz. Known by hobbyists as “optician’s rouge,” its superior polishing qualities have displaced the use of other oxides such as iron oxide and zirconia.
“I like starting off with the good stuff,” John says. “You get what you put in. For instance, I use a diamond wheel, whereas someone else might use a lot of .50/sheet sandpaper. At the end of the year, how much is the difference in investment, really?”
Estimating he has cut and shined at least 1,000 polished rocks in the past year, he lets the results do the talking: “ They’re all sold.”
At Kingsley North, Inc. in Norway, MI, known since 1977 for its lapidary supplies (and Australian opals), Richard Paupore offers these succinct suggestions: “Fastest? Using a vibratory tumbler. Easiest, i.e. lowest learning curve? Rotary tumbling. Most unusual? Dry finishing your hard-to-polish rocks. Best way? Maybe a combination of each, starting with a rotary tumbler for coarse stones, then finishing in a vibrating tumbler.”
“What I wish more people would ask before they start,” John suggests, “is what to use before buying the ‘less expensive’ option first .”
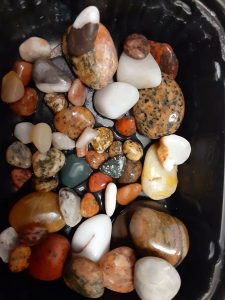
Polished Rocks & Rules
In addition to Minnesota Lapidary Supply, which sells both rotary and vibratory tumblers, MLS owner Val B. Carver owns and operates Blue Gem Agate, whose “sole function” is to sell rocks they personally tumble and polish. He estimates, since 2016, that he’s been tumbling 7,000 pounds a year and 92 different types of polished rocks.
“There’s lots of valid methodologies and few ways to do it ‘wrong,’” Val encourages. Tumbling and techniques have come a long way, leading to what he calls the Nine Golden Rules of rotary tumbling.
Polished Rocks Hacks
Here’s a rockhound hack for getting a shiny finish on polished rocks. Try Borax or Ivory Soap Flakes instead of grit or polish. Use one tablespoon to a three-pound tumbling barrel and run for a couple of hours to achieve a high gloss.
Want to see tumbling in action first? Richard Mueller at Miners Gallery in Alpine, CA, recommends the following steps.
- Tumble stones of similar hardness together.
- Run the tumbler drum ¾ full at all times.
- Size: 1/3 smaller than a marble, 1/3 marble to double thumb-size, 1/3 larger than double thumb-size
- Add abrasive at a rate of 10%, add polish at a rate of 5%, by weight of the dry load.
- Add water to the drum until you see it coming up through the load. If possible, DO NOT USE softened water.
- Run each of the four steps (coarse, medium, fine, polish) for one week.
- Between steps, thoroughly clean rocks and drum. Between last grind/sand step #3 and polish step #4, clean rocks scrupulously (toothbrush suggested) and DO NOT use soap for cleaning.
- Be selective about the rocks you polish. “Garbage in, shiny garbage out.”
- Remember to have FUN.
“There’s no ‘magic bullet.’ You have to do the work and go through the steps,” says Val. “Minnesota agate has been around for a billion years. You have to be as tough as it is to get a result.”
Rush Job
“My process is very different from almost everyone else,” says Bench Tips contributor, Bob Rush. “It involves two steps versus the typical five or six steps.”
He starts by filling a 40-lb., and two 12-lb., barrels with rocks and adding 60-grit tumbling media. “I run it for four to five weeks, empty it out, wash the rocks off, put them back into the barrels with tumbling polish, run for another four to five weeks, and then I’m finished.”
Bob grew up on a farm in southern Oregon where his father “puttered around” with a small tumbler but, as a farmer, didn’t have time to indulge in “frivolous” activity, and he inherited that streamlined sensibility: “Most tumbling suppliers have a method where the tumblers run with a coarse grit and then 220-, 400-, and 600-grits each for a week.”
Typical tumbling involves purchasing and using a spectrum of materials, i.e., grits, while Bob’s process takes less work (and money) by using only the lowest-cost (60-grit) tumbling media. Why it works for him, he says, is the nature of the grit – silicon carbide – which doesn’t generally occur in nature except as the rare mineral, moissanite (SiC).
“It is a man-made abrasive that has a unique quality as it wears down,” Bob says. “The grains of grit do not become more rounded as they wear. They just fracture into smaller pieces, still with sharp edges, so they continue to abrade the rocks in the tumbler.”
The longer the tumbler runs, the finer the grit until, “The grit becomes just gray powder in water, basically a grit slurry.”
Another unique voice to polishing comes from Keith Dull, a top lapidary artist and one of the first to tumble-finish obsidian cabochons to a high-gloss finish.
“Most of the time, I had to quickly add the final gloss by hand, with cerium and wool rug. But once and a while, I was able to achieve it without any additional effort! Mainly, I was impatient and didn’t leave it in the final polish long enough. If I had, then I don’t think I would have ever needed to hand polish!”
Is It Stone Soup Yet?
Val, who co-authored the beginner’s guide, Gemstone Tumbling, Cutting, Drilling & Cabochon Making with Jim Magnuson, says a common question from newbie tumblers is, does putting a shine on really have to take four weeks?
“Versus a million years naturally?” he muses. “I tell ‘em, you’re doing good.”
This story about polished rocks previously appeared in Rock & Gem magazine. Click here to subscribe. Story by L.A Sokolowski.