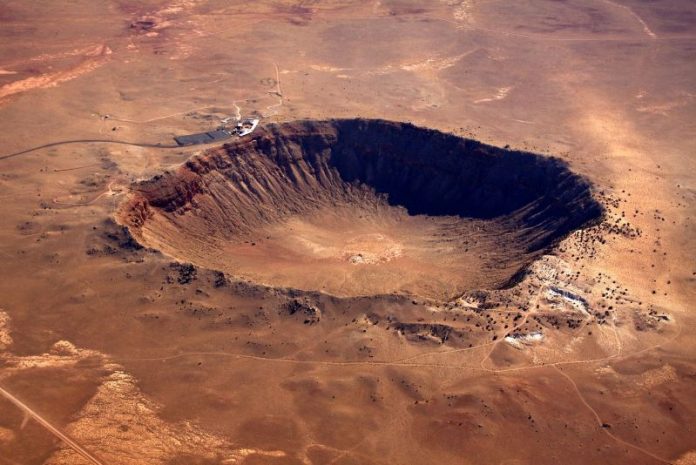
What is moissanite? When a popular artisan who has worked in lapidary since the 1950s suggests taking a closer look at their “grit of choice,” it’s at least worth checking out. Meet moissanite, also known as silicon carbide, a rare natural mineral (SiC). Until the late 1980s, it was believed to only be found in grains of primitive chondrictic meteorites pre-dating the formation of our own Sun but with a 9.25 Mohs rating, a close contender in hardness to diamond and now a popular diamond alternative.
Now that’s interesting.
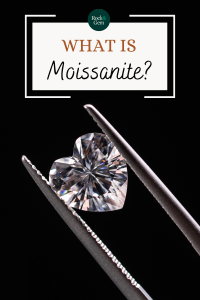
What is Moissanite?
The mineral is named after French chemist and 1906 Nobel Prize recipient Ferdinand Frédéric Henri Moissan, one of the original members of the International Atomic Weights Committee and designer of the electric-arc furnace, which could attain temperatures upwards of 3,500°C (or 6,332°F).
Moissan used his furnace to volatilize, or evaporate, substances heretofore regarded as infusible and impossible to melt down. His work preparing new compounds helped lead to the discovery of the highly abrasive carborundum and afforded him the pursuit of his own theory that diamonds could be synthesized by crystallizing carbon under pressure from molten iron.
That’s right. Monsieur Moissan is a grandperé of the artificial diamond.
In fact, the chemist misidentified what is moissanite when he found natural moissanite as a diamond in 1893 while examining grains of rock samples from a meteor crater in Canyon Diablo outside of Flagstaff, Arizona. The resulting dent in the Earth, nearly a mile wide and 750 feet deep, according to The Barringer Crater Company, was created when a meteor, estimated at 300,000 tons and traveling 26,000 mph, struck with 150 times the force of the atomic bomb at Hiroshima and blanketed the desert for a mile in every direction with pulverized melted rock mixed with fragments of meteoritic iron.
It would take nearly a decade (1905) before Moissan correctly deduced the hexagonal platelets in his crystals as silicon carbide, not diamond, by measuring their density and inertness to chemical reactions, and establishing the natural existence of the mineral on Earth.
Its mineral form would eventually be named in honor of the French chemist, but it was American chemist Edward G. Acheson (also credited with discovering carborundum) who got the jump on what is moissanite by synthesizing artificial silicon carbide, inventing and patenting (Eng Patent 17911) what is still known as the Acheson Process. This gritty breakthrough in manufacturing abrasives is credited with advancing the Industrial Age and helped lead to Acheson’s induction in 1997 into the National Inventors Hall of Fame®.
Natural (non-meteor) moissanite was not found until 1958, in the upper mantel of Wyoming’s Eocene-era Green River Formation, and again in 1963 when American Mineralogist reported its presence in inclusions of rare kimberlite in a Yakutia diamond mine in eastern Russia.
But that didn’t necessarily convince Charles Milton, a Fellow of the Geological Society of America and something of a mineralogical dragon slayer, as his 1990 GSA memorial attests:
“Although he enjoyed the detective work involved in the description of a new mineral, he was equally enthusiastic about discrediting mineral species. To this end, Charlie was deeply involved in the investigation of moissanite and the question of its legitimacy as a mineral. He published on this subject for more than 50 years. Only recently has moissanite (or some polymorph of SiC) been found as a solid inclusion in diamond.”
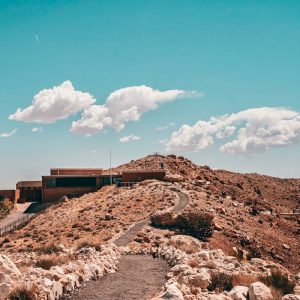
Courtesy Meteor Crater & Barringer Space Museum
What is Moissanite? The Nitty Gritty
Fortunately, what is moissanite is not a debate the average rock tumbler has to worry about. All applications of silicon carbide in use today are synthetic, from diamond alternatives to lapidary grinding wheels to playing a key role in the semiconductor industry.
Whether sharpening knives or smoothing stones, the “Cadillac of abrasive grits,” as Armour Products refers to silicon carbide, is produced by mixing silica (SiO2) with carbon (C) — basically sand and coal — in electric resistance furnaces at temperatures akin to Moisson: between 1,600°C (2,190°F) and 2,500°C (4,530°F).
Technology manufacturer Arrow ECS explains that darker versions of silicon carbide usually include iron and carbon impurities, but pure SiC crystals are colorless, forming when silicon carbide sublimes (changes to vapor when heated and forms a solid again after cooling).
Silicon carbide is then crushed and screened into sizes ranging from grits to powders for sandblasting, cutting, grinding and polishing. “Graded” grit contains particles all closely matched in size.
The Barringer Meteor Crater & Space MuseumWe’re all made of a little stardust, so while those rocks are tumbling in their silicon carbide, consider a trip to Winslow, Arizona to see and learn more about the crater impact site where Henri Moissan first found his intergalactic namesake. The Crater lies at 5,640’ above sea level, is over a mile wide and 560’ deep, and surrounded by a rim that rises 148’ above the surrounding plains. The middle of the crater is filled with eroded rubble lying above crater bedrock. Named a 2021 TripAdvisor Travellers’ Choice and a 2020 Condé Nast Traveller Seven Wonders Of The World, The Barringer Meteor Crater & Space Museum features daily (8 a.m. to 6 p.m.) interactive displays about the Earth and space science, including a 4D movie, Collision! plus guided rim tours, viewing platforms, and walking paths that deliver spectacular views of this natural wonder. Admission supports the preservation of the site and supports scientific research in the field of meteoritics. Visit MeteorCrater.com. More information on the Barringer Meteor Crater can be found in this issue in the Rock Science section starting on page 68. |
But let’s get to the nitty gritty. When it comes to tumbling and finishing, silicon carbide grit rubs everybody – rock tumblers, gem cutters and lapidary artists – the right way.
Why? Three good reasons:
- It’s hard. With a Mohs scale hardness of more than nine, it is ideal to cut tumbling roughs like agate, jasper and petrified wood. Harder rocks like beryl and topaz need more time tumbled in coarse grit than softer materials (like obsidian or sodalite).
- It crushes into sharp, angular particles. That increases cutting and grinding efficiency as it tumbles between rocks in a barrel.
- It’s not expensive. Retail sites like RockTumbler.com cite silicon carbide as selling, as a screened and packaged product, for just a few dollars a pound.
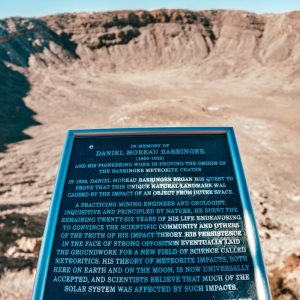
Courtesy Meteor Crater & Barringer Space Museum
Grit size (the higher the number, the finer the grit) impacts both the rocks to be polished and the fortitude of the barrel used. Shaping grit (60/90) is considered the most coarse and is used with rocks during the first tumbler stage to round off rough and sharp edges before moving to a medium/fine grit (120/220) to remove scratches, cracks and dimples.
The topic of size prompted a gritty Facebook discussion on a Rock Tumbling & Polishing Group earlier in the summer, regarding 10 pounds of an unidentified but “very coarse” silicon carbide grit one of its members had received for free (can’t get more ‘not expensive’ than that).
Posting a photo of the mystery grit next to a finer but still Stage 1 silicon carbide for comparison, they asked, “Is this stuff useable or is it too extreme?” They guessed the grit size as 10 or 12 and hoped to test it out as a “fast cut” on some “expendable stones” in a dual barrel three-pound tumbler.
Advice tumbled in: “I used stuff that looked like that. On harder rocks it was awesome. It seemed to get them round quicker but on softer rocks it ground them too quickly into nothing. It scratches the inside of the barrel pretty bad, so I assume it wears out faster.”
“I tried 46/70 in my three-pound tumbler. It removed a lot and left an ugly surface on more delicate stones. So if you want to remove the surface it will probably work, but won’t eliminate the need for using 60/90 as the next stage. And don’t use it on anything delicate. I understand larger barrels create a more aggressive effect due to the weight of rocks pushing down.”
“Coarse grit in three-pound barrels is ineffective, too few particles due to size. It won’t hurt the barrel. I run 45/70 in three-pound barrels for some agates but it’s no faster than 60/90. I use it because I have it!”
“It looks like 36 grit. It won’t wear out barrels any quicker but will not work well in small barrels. I have used it in 12-pound barrels for Stage One with Bahia agate. Overall, pretty useless in small tumblers.”
“I think it would be great to quickly wear down agates with lots of pock marks, etc.”
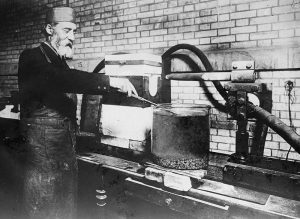
Courtesy Public Domain US/US Library of Congress Prints & Photographs
Time to Shine
Henri Moissan was probably not thinking about tumbling when he deduced silicon carbonate from iron meteorite samples in the Arizona desert 130 years ago. But his patient approach to what is moissanite and shining a light on scientific inquiry is not so different from today’s methodical steps toward shining stones:
“The advancement of science is slow; it is effected only by virtue of hard work and perseverance.”
You might want to add… a little grit.
This story about what is moissanite previously appeared in Rock & Gem magazine. Click here to subscribe. Story by L.A Sokolowski.