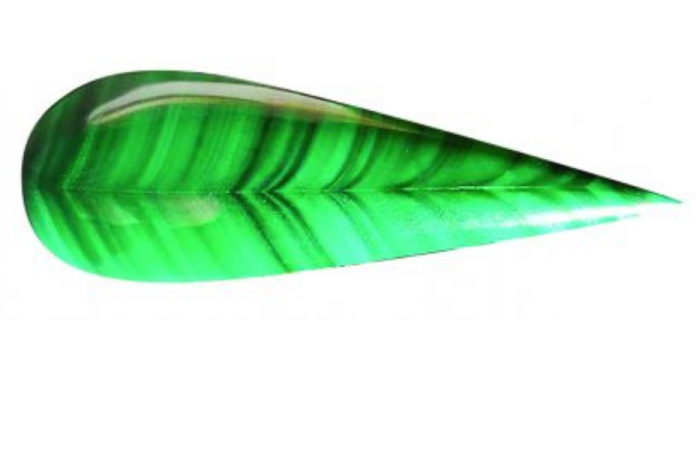
Malachite is one of the most used stones in lapidary and has been for over 3,000 years. It can be found all over the globe, but the main types you generally see are from the Congo, Africa, and Arizona.
Its bright green colors and patterns highly attract attention. Being a mineral of copper, it can be found in many different fashions and variations. Malachite is generally found as light and dark green bands, usually composed in botryoidal chunks. It can also be found in microcrystal form, as well as mixed with other copper minerals such as azurite and chrysocolla/gem silica.
Patterns Draw Interest In Malachite
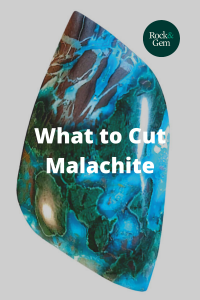
Many seek out the fan patterns that are chatoyant or orb patterns in the highly botryoidal stones. No matter what your preference is, malachite will make some outstanding cabochons.
Shopping for malachite is fairly easy, it can be found online or at just about any gem show, however, picking out the best pieces could be a challenge. For the experienced buyer, looking for rough might be the best for your value and cutting it into slabs yourself. For beginners, buying slabs might be the way to get started until you get more familiar with this material. Malachite tends to have many vugs throughout the rough material, which leads to workarounds.
So when buying rough, anticipate many vug openings inside that you will either need to incorporate into your designs or cut around and cab the solid pieces. When working with malachite mixtures combined with other copper ore materials, be aware of the hardness differences that tend to undercut and leave uneven surfaces on your cabochons.
Type Determines Complexity of Work
Cabbing malachite can be simple or complex depending on the type you are working with. Congo malachite is rather soft and shapes fairly easily, but when working with malachite mixed with other copper minerals from areas like Arizona, it could lead to a slight challenge in dealing with the hardness differences.
If the malachite is mixed with azurite or chrysocolla, stick with your general cabbing process, however, if it’s mixed with any type of chalcedony beware of the undercutting issue. This is where you really want to take your time and work on shaping and smoothing the dome of your cab on the steel wheels before moving on to the soft resin wheels. I like to shape and dome on the 80 grit, and then smooth it out with 180 and 220 grit steel wheels, removing any deep scratches and flat spots as possible.
Once you are ready to move on to the 280 grit wheel, cab with more of a light touch trying not to push too hard to avoid deep undercutting, where the softer material grinds down lower than the harder chalcedony, leaving you with an uneven surface across the top of your cab. Malachite takes a wonderful polish easily on the wheels up to 14k grit, but you can add to the shine with a little Zam compound to enhance the mirror polish.
Take Precautions During Polishing
One thing to always be aware of about malachite it is safe to handle as polished specimens, but working with this material you should ALWAYS wear a respirator mask, as the dust is extremely toxic. I wouldn’t suggest a paper painter’s mask, when working with this material I would suggest no less than an N95 or P100 respirator mask to be on the safe side.
Always have plenty of water flowing in your machines, but just because you think you have good water flow, don’t assume it’s safe to cab without a mask, the mist will contain the malachite particles which you can breathe in.