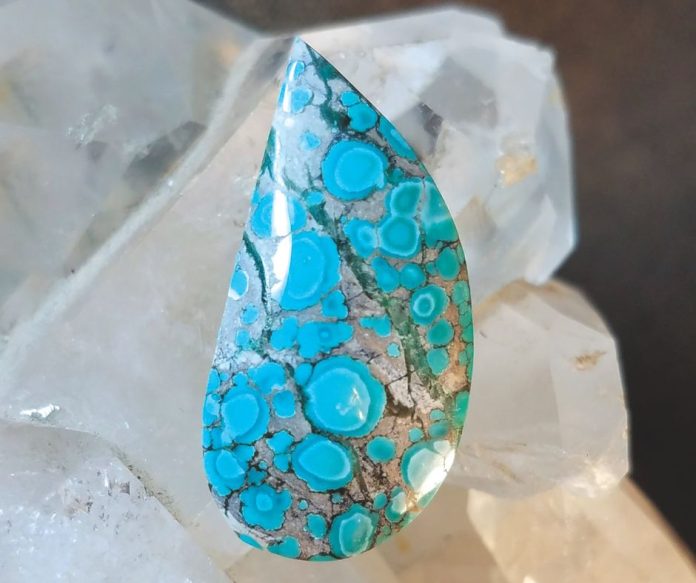
A turquoise cabochon and turquoise jewelry, in general, uses one of the most prestigious stones in lapidary. It’s been used for thousands of years. It was even used in King Tut’s burial mask in Ancient Egypt. It can be found in almost all regions of the world from Turkey and China to North America. Colored by copper, the colors in turquoise range from blue to green.
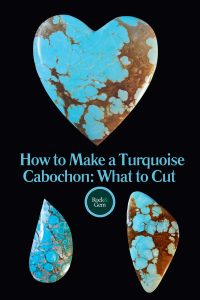
Turquoise has a hardness of 5 to 6 on the Mohs scale. The most sought turquoise is usually the evenly balanced single-colored stones or specimens with spider webbing and some matrix showing.
Finding the Best Slabs
Over the years, turquoise has seemingly lost some value because of treatments and imitations that flood the market. There are many examples of turquoise becoming extremely rare. This is because of the closures of mines or through the process of depletion. When purchasing material for a turquoise cabochon, it can be very hard to tell what you will get by purchasing rough material. What you see on the outside can be entirely different from what you get once it’s cut and polished. If you are new to cutting turquoise, it might be best to find cut slabs. This will allow you to see what the material will look like.
Many times turquoise can be just on the surface and not run all the way through the stone. But by buying already cut material, you can alleviate buying something unusable or picking up something that has too much waste material. This is especially true since you are buying turquoise cabochon material by the pound.
Another thing to always ask when purchasing is whether the material has been stabilized. The majority of all turquoise nowadays has been stabilized, but if you find the natural material you will have to consider an entirely different perspective and greater patience when cutting and cabbing this material.
Making a Turquoise Cabochon: Using a Gentle Approach
Slabbing for a turquoise cabochon is usually best done by hand cutting on a smaller saw using a very thin blade. Many will say using a thin blade saves you from wasting too much of the material, and this is true. However, the benefit of using a thinner blade, in this case, is a less aggressive blade running through your sensitive material. This keeps the vibrations down so the material doesn’t break apart during cutting.
Over the years, I have discussed the cabbing process with many cabochon cutters, and there seem to be many different ways to approach cabbing this material. For anyone cutting turquoise for the first time, let me suggest, finding stabilized material to get a feel for how it cuts. I would always start on a less aggressive wheel, usually a 220 steel to shape your preform and start the doming process. I like using the 220 soft resin Nova wheel to gently smooth it out and remove material to keep from creating flat spots.
Take a gentle approach and carefully watch how much material is being removed. Remember, this is a delicate and soft material that you can potentially grind through in a hurry or crumble to pieces. Take the usual steps to finish your turquoise cabochon by using 600, 1200 and 14k grit wheels.
Finishing Turquoise
The finishing process has a bunch of different options. I like to go up to a 50k grit Nova wheel and use a white jeweler’s rouge if needed. Some may use Zam polishing compounds, but it depends on the type of turquoise you are using.
This column about making a turquoise cabochon previously appeared in Rock & Gem magazine. Click here to subscribe. Column by Russ Kaniuth.